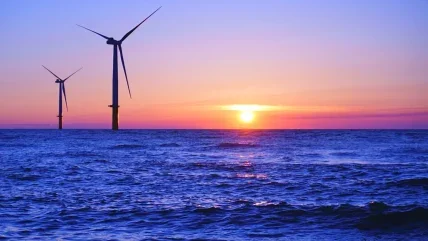
In up to 25m of water with a firm seabed, the monopile foundation’s proven design has long been the default choice over contenders such as gravity bases. Its shape lends itself to simple calculations, straightforward fabrication and tight packing on transport vessels. These giant steel pipes range from 2.5-6.0m in diameter, are 50-60m long and weigh around 500t, although on deeper sites they can weigh in excess of 800t.
Installation involves hammering the monopile into the seabed, then sliding a transition piece (TP) on top, to which the turbine’s tower and the rest of the required equipment (access ladders, J-tubes, crane) can be bolted. To fix the TP in place, grout (high-strength, fast-curing cement) is injected into the annular gap between the TP and monopile. This three-stage process lets the installer correct the TP’s angle to true vertical, and place it at exactly the right height above the sea.
Monopiles: not a universal solution
"The wind business likes monopiles," says Olaf Beeg, package manager for civil works at Vattenfall’s Dan Tysk field in the German North Sea. "It’s a reliable and simple technology that is quick and cheap to fabricate and install."
The monopile, however, is neither perfect nor a universal solution. It requires extra scour protection around its base and the noisy piling has attracted installation restrictions. Grouting is difficult in cold conditions, while problems with crumbling grout have also required expensive remedial action post-installation. These days, new TP attachment methods have appeared that employ vertical and horizontal shear keys, along with conical (and even bolted) connections.
"Basing connections only on friction between the grout and steel meant that they would not last for a long time," says Beeg. "Dynamic loads meant it was like loosening a fence post. Now, the connection is much more sophisticated."
Monopiles attract high-hydrodynamic loads from the water and, as water depths and the size of mounted turbines increase, the diameter of pile required to resist static and dynamic forces from the sea, wind and turbine becomes much larger – and therefore more awkward to fabricate, transport and install.
"Traditionally, a 5-6MW turbine in depths of 25-30m would be borderline for the largest monopile," says Beeg. Vattenfall’s Dan Tysk field, which is currently under construction, employs 6m-diameter monopiles. "These are already heavy," Beeg notes.
Deep-water jackets
At depths greater than 25m, developers have traditionally preferred the dominant deep-water foundation: the jacket. It is to jackets that they look to handle mid-to-deep waters (30-60m), which are the upcoming challenge in the UK’s massive Round 3 wind farms.
Jackets can take a number of forms with various footing options, but those deployed so far have been four-sided, A-shaped, truss-like lattice structures of low-diameter steel tubes, resting on piles and typically weighing around 500-600t. Immensely strong and with a proven track record over decades of use in the offshore oil and gas industry, their low risk alone sells them to developers.
But, with their intricate, multipipe welded joints, jackets are time-consuming to build and coat with anticorrosion treatments. Each individual turbine location demands a custom-made jacket to match its seabed and water depth, and jackets cannot be easily stacked for sea transport. All this adds up to a more expensive proposition than monopiles. "Handcrafting is not the most economical way to do it and the UK will need a huge number of jackets for Round 3," observes Beeg, adding that Vattenfall’s next UK project alone will require 200 jackets.
"The industry needs a way to ‘productionise’ jackets and adjust them for water depth, rather than producing an individual design for each location," states Colin Pearce, renewables business development manager at Houlder.
Designs such as those by Atkins/BiFab and WindSea, and OWEC Tower’s Quattropod aim to simplify the structure and make it more suitable for mass production. Vattenfall’s UK-based Ormonde and C-Power’s Thornton Bank in Belgium are the first high-volume deployments of the Quattropod; the others are unproven.
There is also WeserWind’s VARIOBASE design, which employs cast steel nodes instead of complex, multipipe, welded joints. This approach lets the fabricator use automated welding to connect simple pipes. But, despite saving manufacturing time, the overall cost is higher than conventionally welded jackets. Only one onshore VARIOBASE demonstrator has been built.
"This is a promising concept," says Beeg. "But it’s expensive to build the moulds, so you need high volumes and large orders."
The Carbon Trust’s Offshore Wind Accelerator programme has encouraged other cost-effective designs such as Keystone’s twisted jacket. With fewer welds and less steel than traditional designs, this three-legged variant is easier to fabricate and more units can be packed onto an installation vessel.
Techniques such as pre-piling also help to bring down jacket installation costs. This involves preinstalling piles through a reusable template; the jacket is then dropped onto them and grouted into position. Using this method, piling on Ormonde took a few hours compared with three to four days on Alpha Ventus, another of Vattenfall’s fields.
XL monopiles
Despite these advances, the jacket’s deeper-water dominance is now threatened by the emergence of ‘XL’ monopiles. Up to 10m in diameter, these may be used at depths in excess of 40m. "The next Vattenfall project in the German Bight will use monopiles in water depths of up to 37m," says Beeg. "The trend is clear: up to 40m is feasible."
Pearce is slightly more conservative. "Monopiles are definitely increasing in size and weight," he acknowledges.
"Most people see the limit at around 32-35m of water at the moment."
In June 2013, however, German fabricator EEW SPC produced a 10m-diameter pipe section and is expecting to receive its first orders for 9m-diameter monopiles shortly.
These giant monopiles require greater wall thickness in order to cope with wave forces and resist buckling loads during piling; EEW’s test piece used a 95mm plate.
So could monopiles extend their offshore supremacy to deeper waters? First, a host of challenges must be overcome, starting with the lifting process: how do you hold a 1,000-1,200t tube without damaging it? A hydraulic gripper is the answer, but this presents another design hurdle.
"There’s not always enough thought given to handling monopiles," says Pearce. "You have to be gentle with them. There’s a risk of localised buckling or even puncture through the skin if you grip them too tightly in a small area. There’s also a greater risk of ovality if they are stored horizontally."
Finding a suitable installation vessel that can lift XL monopiles is another challenge. "Fabrication is the current bottleneck and transportation will be the next one," says Beeg. "With 1,000t piles, we are limited by crane capacity. Not many jack-ups could handle those weights."
According to Pearce, that means moving to semisubmersible-based cranes, which give a big step up in capacity – and cost. These heavy-lift vessels are scarce and, he claims, "an order of magnitude" more expensive, potentially cancelling out much of the XL’s cost benefits.
However, consultancies such as Houlder are examining ways to get around these handling challenges and, according to Beeg, XL monopiles are economically feasible despite these issues. Jackets and monopiles remain the only two proven contenders for deeper-water foundations. As ever, the choice will come down to the cost per installed megawatt.