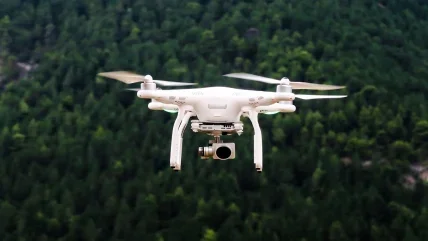
The history of offshore wind isn’t a particularly long read – it has only been around for about 30 years, with the first commercial offshore windfarm having been built off the coast of Vindeby, Denmark, in 1991. In the US, the first offshore wind farm – the Block Island Wind Farm, just off the coast of Rhode Island – was only erected in 2016, just a few years ago. However, now that the industry’s early days are behind it, its focus is shifting from new installations to the maintenance and operation of existing turbines.
And when it comes to maintenance and turbine inspection, offshore wind turbines are exposed to a considerably more challenging environment while also being far more difficult for operators to reach. As a result, the industry is constantly looking into new technologies to make these processes easier, more comprehensive and safer for the maintenance personnel who have to carry the work out. Across the sector, one of the technologies that operators are looking into are drones that can monitor turbines for flaws and faults as they develop, increasing the speed at which these faults can be detected and helping to reduce maintenance time in turn. This technology can be further enhanced by pairing it with autonomous or semi-autonomous systems, which can enable drones to carry out a number of tasks without the direct control of an operator, streamlining the monitoring process.
“Ultimately, cost savings and safety are the two things that operators are seeing value in,” explains Michael Corsar, chief technology officer at Innvotek, an innovation consultancy with an engineering team focused on robotic and automation solution development. A study published in Results in Engineering found that replacing rope-access inspection with drones can reduce costs by up to 70% and decrease revenue lost due to downtime by up to 90%.
70%
The potential cost reduction by replacing rope-access inspection of offshore wind turbines with drones.
90%
The potential decrease in lost revenue due to down-time during inspection.
Results in Engineering
Offshore automation
Innvotek have launched a number of products in this area over the past few years, most notably its Firefly Inspect and Amphibian systems. As Corsar says, cost savings and safety are among the benefits these technologies can provide, which are of particular interest to the industry for a number of reasons.
“In terms of cost savings, it is very expensive to work offshore. And that’s really driving a lot of the cost of operations and maintenance,” notes Corsar. “In offshore wind, there has been a massive focus on reducing CapEX to bring electricity costs in line with what’s affordable. But now, I think probably 50% of the O&M budget is spent on turbine inspection and maintenance, and offshore logistics – so, the costs of sending people offshore are enormous.”
With that in mind, Corsar is keen to stress that the Innvotek’s drones are not looking to replace people working in offshore wind, noting that instead the company’s products look to reduce the amount of time personnel spend offshore.
“You can get the robot to do the highly boring, monotonous, long-duration tasks. And you can get the people to do the much more skilled, dexterous or difficult tasks – that’s kind of the ideal combination,” he says. “I think the technology is at a place where operators are now starting to see the value there.”
Safety, of course, is another key driver of autonomous and semi-autonomous drone technology in the wind power industry. This doesn’t just mean keeping workers safe, but also providing them with good working conditions. As Corsar notes, “On an offshore wind turbine, I don’t think there’s anywhere that’s designated as a non-hazardous area.”
It’s a demanding environment for personnel, many of whom are working 12-hour shifts. If drone technologies like Innvotek’s can help reduce the time required to carry out this work, it could potentially improve people’s welfare, reduce the likelihood of accidents and save significant costs on maintenance.
Product of collaboration
Of course, everything goes smoother when you have people to help you. For Innvotek, they’ve been able to collaborate on both the Firefly Inspect and Amphibian systems with the Offshore Renewable Energy (ORE) Catapult, the UK’s leading technology innovation centre for offshore wind, wave and tidal energy.
“We’ve collaborated with the Catapult on a variety of things, including Firefly. They’ve been a great partner, because their overview of the offshore wind market is massive, as are their connections,” says Corsar. “But their test facilities are unrivalled as well. And it was really the ability to test our technology at full scale at their facilities [which] brought us to see them.”
Due to this partnership, Innvotek was able to take the Firefly Inspect system up to the ORE Catapult’s National Renewable Energy Centre in Blyth during its testing and validation phase of R&D, and spent several days inspecting one of the Catapult’s wind turbine blades. Firefly Inspect consists of a set of flight control algorithms that give semi-autonomous control to drone systems. These drones carry an active thermography system, which can penetrate the surface layers and see defects that are relatively deep within the composite material that the blades are made from. This can’t be achieved using normal photography alone, which can only capture surface-level defects.
The Firefly’s autonomous capabilities enable it to generate a flight path, fly it, log where it is at any one time and then assemble the data in a way that’s easy for the operators to sort through later. With most current drone inspections, much of the data handling is manual, which can take an enormous amount of time. The Firefly knows where it is and appends that information to the thermographic images, making it easy to sort through defects. Rather than looking through the entire blade that will be in mostly good condition, operators can just focus on the bits that are potentially defective. The thermography technology the Firefly uses has been applied in other industries in the past, but mainly in a factory setting with a fixed production environment. As far as Corsar is aware, Innvotek is the first company to put this technology on a drone and use it to inspect a wind turbine blade.
“We’re definitely seeing a step up in capability compared with typical close visual inspection that most drone inspections conduct,” he adds. “We can see defects that are forming under the surface of the blade that may well break out in the future, which would potentially give operators prior warning of damage before it actually becomes significant and needs to be repaired. And, obviously, that gives people time to plan maintenance rather than just react to it.”
On air and sea
Innvotek also collaborates with the ORE Catapult on its Amphibian project – a tethered crawler designed for splash zones down to -60m subsea, using powerful magnets to crawl on the surface of monopiles. The robotic inspection platform provides access to the interface between the air and the sea, where waves make contact with the turbine. This area has its own challenges, and structures see high levels of corrosion here due to the amount of oxygen exposure they receive from the waves, not to mention the effects of the seawater itself.
In offshore wind, most turbines have monopile foundations, which are essentially large piles driven into the seabed. These monopiles have to deal with a considerable amount of corrosion, so there’s a big need for inspection – both internally and externally. However, due to the nature of the sea, it can be very difficult to access these piles. For the same reason, companies are reluctant to send out divers. Remotely-operated underwater vehicles (ROVs) present their own challenges – mainly that they’re expensive and can’t be accessed from above using scaffolding or rope access. Amphibian, on the hand, allows operators to come from the air and work downwards from the top of the transition piece, inspecting as it goes down the monopile, and provides full access to the foundation.
“We can do all sorts of visual inspections, but also more advanced non-destructive testing as well,” says Corsar. “And we can do cleaning. Monopiles are subjected to a lot of biofouling, which adds a lot of weight to the foundation due to the build up of marine growth.” This can result in a reduced lifespan. Looking to address this issue, Amphibian provides a dual-purpose service by cleaning the monopile foundations before inspecting for faults. Innvotek has classed the Amphibian as an ‘operator aid’ that looks to reduce cognitive load as, typically, it will be operated for long durations. In this sense, anything that the robot can do without human input is a benefit. As a result, it has an automatic heading control – once it’s set off in one direction, it will keep going until it’s told to stop.
“Once you’re in position, you might have to deploy [the Amphibian] from the top side on a transition piece, and you’ve got to navigate down to the waterline,” says Corsar. “You can then input the automated scanning plan, and it’ll go off and clean and inspect automatically as well.”
Beyond Firefly Inspect and Amphibian, Innvotek is involved in what Corsar describes as “a very interesting proof of concept” in collaboration with a wind turbine OEM. The application is around the automated tensioning of generator bolts in service – looking directly at maintenance rather than inspection.
“Bolt tensioning is a massive issue for maintenance teams,” says Corsar. “Typical wind turbines might have 6,000 critical bolts, and in service, they can come loose.” It’s a maintenance item that has to be dealt with on a regular interval, typically two to three years. The robot that Innvotek is developing will be able to inspect and then torque up a wind turbine’s generator bolts.
The cost of innovation
In the meantime, the main challenge that Innvotek faces is one that many in the industry will be able to relate to – getting the funding together to bring their projects to fruition. Even after all the testing and R&D is carried out, and a proof of concept is developed, there’s a big step change and budget requirement in order to test these technologies offshore. And that’s not even taking into account the challenges presented by offshore testing itself – for example, finding a suitable weather window in which to carry out testing. When a good weather window is available, offshore operators will typically be looking to conduct their own maintenance work, rather than making their turbines available for testing.
Corsar notes the importance of not viewing the industry as a monolith – within OEM teams and elsewhere, everyone has their own motivations, which can frequently hinder innovation and progress. “But there’s definitely a lot of champions for our type of technology in the wind industry,” he adds. “And I think, along with a lot of contemporaries and other companies who are now in this space, there’s a general consensus that we’re getting there – but it’s definitely slow.”
Part of that issue, ironically, is that Innvotek has found considerably more traction among the oil and gas industry, which in turn has enabled it to leapfrog into offshore wind, though this system would seem at odds with the wind power mentality.
This is due, in part, to the relative youth of offshore wind, which doesn’t have the same history of asset fabric maintenance and integrity management that those in oil and gas do. “It’s a question of that maturing, and therefore having a baseline industry standards as to what is acceptable technology and what’s still to be proven,” says Corsar. Looking ahead to the future, Innvotek’s work in the area of automation in wind turbine inspection and maintenance is beginning to turn to resident robotics and how to control these systems from the shore. “We’re starting to work with other companies on an ecosystem of robotics, which can plug into a satellite communication system that can then allow control from an onshore control room – actually real-time control of robots offshore,” he says.
This would extend to drones and other mobile platforms as well. While still in its nascency, the potential around being able to conduct inspections completely remotely is huge, and Corsar sees that capability as the ultimate goal for the company in the next five to ten years. With many offshore wind operators today now turning to autonomous and semi-autonomous drone systems to carry out the inspection of their turbines, this long-distance control could well see the same interest by the end of this decade. Only time will tell.